Cheese processing line manufacturer GEA De Klokslag has recently put the finishing touch on cheese production lines and pickle installations in the cheese factory of the A-ware Food Group in Heerenveen. At this location the factory will annually produce 80,000 tons of typical Dutch cheese from 2015 onward. Via GEA De Klokslag SEW-EURODRIVE is involved in the project as the supplier of many drives.
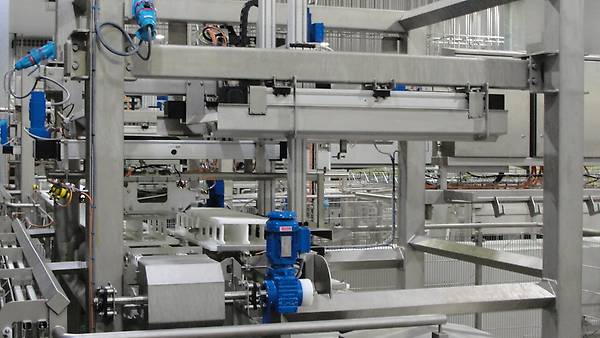
GEA De Klokslag Engineering from Bolsward is an expert in designing and building cheese production systems. The systems are used in cheese factories. “Very often these are enormous companies”, states managing director Evert Yntema from GEA De Klokslag: “We have provided cheese factories with our systems before, amongst others Molkerei Ammerland in Dringenburg and DMK in Edewecht (both situated in Germany), projects with a capacity of approx. 1,6 billion liter milk per year.”
“The delivery of the cheese production lines and pickle installations for the A-ware Food Group cheese factory is one of the biggest orders in our company’s history”, says Yntema. “We are very proud that as Friesians we were able to contribute to this A-ware factory in Friesian Heerenveen.”
The first cheese was immersed in the pickle bath on 3 December 2014 under the supervision of the A-ware Food Group founders’ offspring. Under conditioned circumstances the group takes care of the riping, cutting, packing and storing of the cheese, and finally also for the transport in Europe and, more often across European borders.
GEA De Klokslag developed the entire production line: Milk entry, pre-factory, cheese room, control and ice water installation. It also thought along with regard to the design of the process installations. At this stage an appeal was also made to SEW-EURODRIVE for the drive and control of the lines.
Large quantities of SEW products can be found in the new cheese factory: MOVITRAC® frequency inverters, MOVIDRIVE® application inverters, CMP servo motors – in various cheese and barrel transfers and cover placers. Moreover there are CMSB servo cylinders with hubs of 800 mm (!) for the transport of barrels in the press lines and DR.. squirrel cage induction motors.
GEA De Klokslag opted purposefully for the application of more servo drives. The machine cycle times become shorter, so the movements must be faster. Accurate positioning by motor-encoder is now possible instead of positioning by means of an external track encoder. There is a larger speed control range. The control is easier through the bus positioning application module, there are less mechanical components and the own weight is lower as the motors move along often.
Henk Krijger, head of mechanical engineering with GEA De Klokslag is satisfied with SEW’s input: ”We have more than 20 years of experience doing business with SEW, and our connections are fine. We wanted to do more with servo techniques, and SEW has a lot of experience in this field, so opting for SEW-EURODRIVE was logical.”
Roy Burger, sales engineer and SEW’s contact for GEA De Klokslag during a recent tour in the cheese production: “Very impressive. After all the efforts, calculations, selections and quotations it is fantastic to see the installations in real life now.”
Contact: Roy Burger
Components
Feel free to contact us!
Do you need advice on a specific application? Just send us a message with your questions.
Inquire now